Überblick
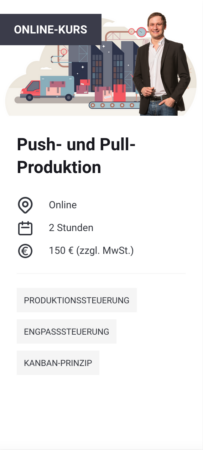
Konzept
- hoher Standardisierungsgrad der Produkte
- flexible Produktion mit kleinen Losgrößen und geringen Rüstzeiten
- nachvollziehbares Behälter- und Lagermanagement
- geglättete Produktion

Sind diese Voraussetzungen erfüllt, kann in der Regel auf ein Kanban-System umgestellt werden. Dabei sind zunächst einige Parameter zur Berechnung des Kanbans notwendig. Hierbei geht es um Daten wie Verbrauch, Wiederbeschaffungszeit, Behältergröße, Sicherheitspuffer und den Meldebestand. Auf dieser Basis kann dann die Anzahl der Kanbans im System ermittelt werden.
Es wird bei der Verwendung von Kanbans so vorgegangen, dass eine Produktionsstufe solange aus Behältern die Vormaterialien entnimmt bis der Meldebestand erreicht wird. Mit diesem erscheint eine kleine Karte (Kanban) mit allen notwendigen Informationen für die vorgelagerte Produktionsstufe. Der Kanban wird also entgegen der Produktionsrichtung verschickt, wodurch die Vorstufe den Auftrag zu Wiederbefüllung der Behälter erhält. Dadurch steuert sich die Produktion weitestgehend ohne einen Eingriff von Außen.
Mehrwert
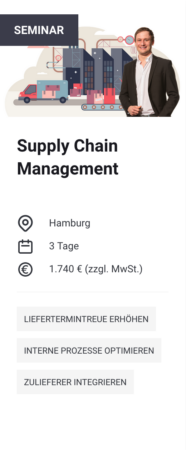